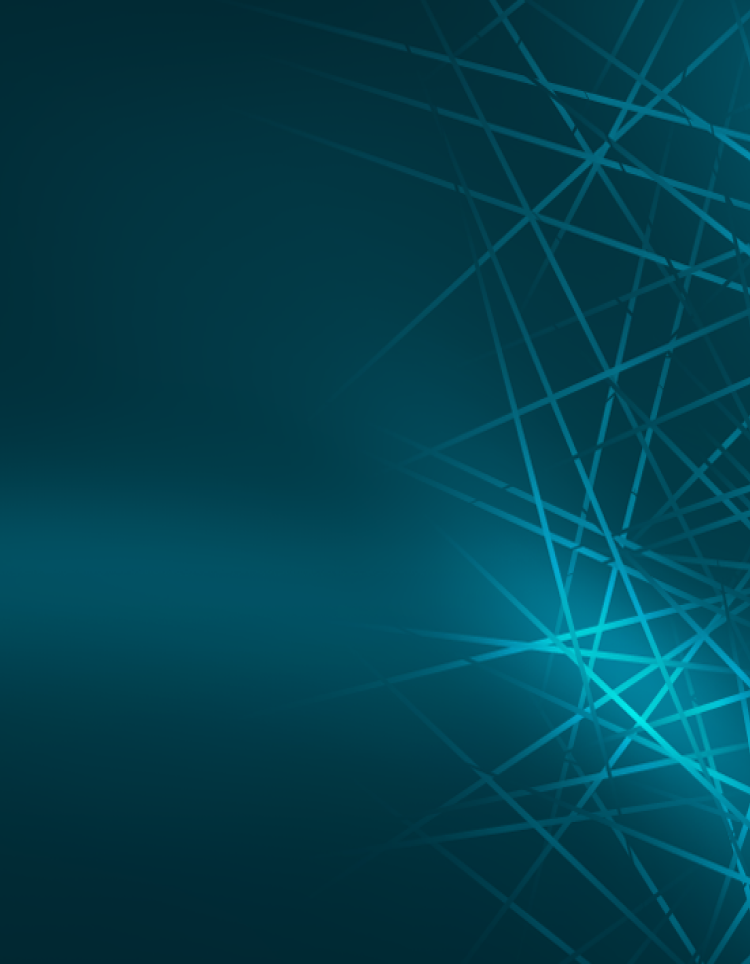
Nanofibres are the technology of future: What is their attractiveness and where do they help?
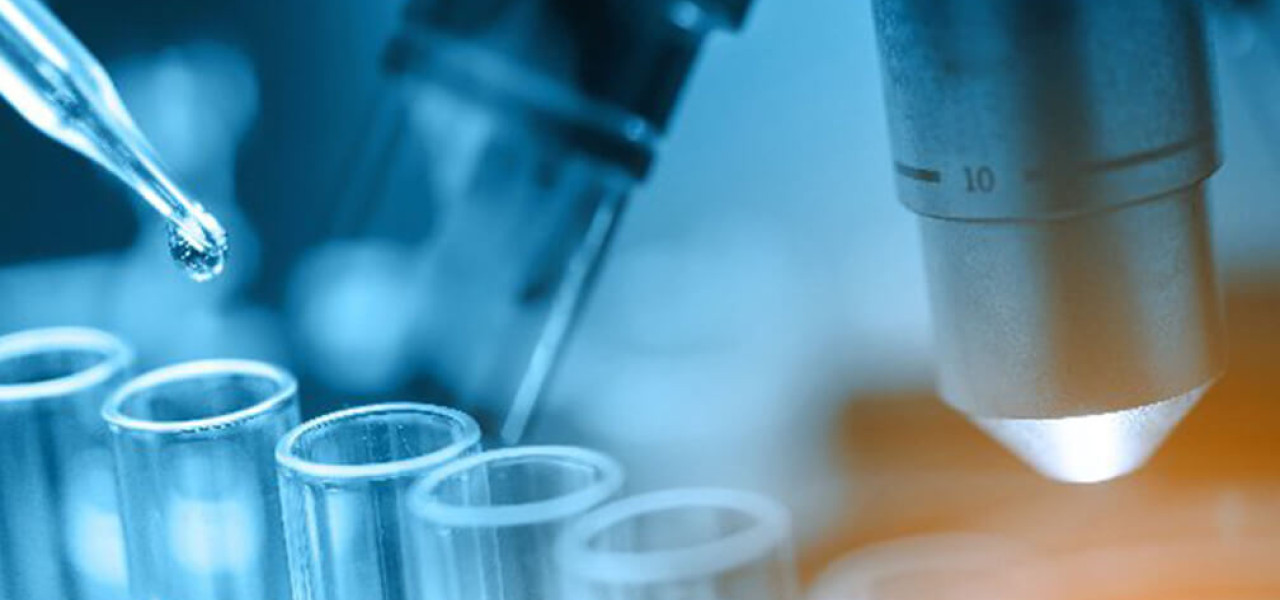
Nanofibres have been with us for hundreds of years. As early as 1600, William Gilbert observed the behaviour of a fluid affected by electric field created by friction of a piece of amber. In 1887, the British physicist Charles Vernon Boys published a manuscript on the development of nanofibres and how they could be produced. His discoveries subsequently helped the American inventor, John Francis Cooley, to file the first modern patent for electrospinning. This was the year 1900.
The 20th century was a period of major development. Between 1934 and 1944, Anton Formhals patented many improved processes for the production of nanofibre‑enriched textile yarns. In 1938, a pair of scientists, Nathalia Rozenblum and Igor Petrjanov‑Sokolov, managed to use electrostatic spinning to produce an ultra‑fine filter, also known as the Petrjanov Filter.
Between 1964 and 1969, Sir Geoffrey Ingram Taylor created the theoretical basis for electrostatic spinning. In the early 1990s, Reneker and Rutledge proved that a variety of polymers could be used to spin nanofibres. Since then, the number of publications on electrospinning has increased exponentially each year.
The revolution in electrospinning came in 2004 at the Technical University in Liberec, where Professor Jirsák's team carried out the Liquid Free Surface Electrospinning. In 2006, together with the company Elmarco, the first industrial machine with a working width of 1600 mm was sold. The Nanospider technology is rightly considered a breakthrough, mainly due to the possibility to produce nanofibres on a truly industrial scale. All this thanks to the simplicity, reliability and flexibility of the raw materials.
Public interest in nanofibre technologies has increased the most due to face masks and respirator filters, but they have already simplified and improved our lives for years.
Why are nanofibres so valued and where do they help?
Nanofibres with diameter measured in nanometers can be made from a variety of polymers and therefore can achieve various physical properties and application potential. All polymer nanofibres are unique due to their large surface‑to-volume ratio, high porosity, noticeable mechanical strength and flexibility compared to their microfibre counterparts.
If you are looking for a material that is both durable and flexible, nanofibre is a clear choice.
Compared to conventional fibres, nanofibres are lightweight, have a small diameter and variable pore structure, making them ideal for use in a variety of industries, such as air filtration, liquid filtration, protective clothing manufacturing, tissue engineering, functional materials manufacturing and energy storage.
In addition, they are so variable that they can be made of both synthetic and natural materials. There are, for example, carbon, polymer, graphite, collagen or cellulose nanofibres, and we have not yet listed all the alternatives.
Where do the nanofibres help?
Thanks to their unique physical properties, nanofibres can be used in many areas of human activity. It's not just ultra‑fine masks and filters for respirators – nanofibres are helping also elsewhere.
Air filtration
By simply adding thin coatings of electrospun nanofibers to traditional filtration substrates, the filtration performance is enhanced several fold. Nanofibers dramatically improve filtration efficiency, they have low initial and persistent pressure drop and enables possibility to optimize the interaction between flow, efficiency and filter life.
Liquid filtration
In the field of liquid filtration, nanofibre membranes with pores capable of capturing even the smallest harmful particles are used. Due to the high surface‑to-volume ratio and the noticeable surface tension, particles smaller than 1 micrometer are captured.
Nanofibre filter technology helps, among other things, in third world countries, where it is necessary to filter polluted water so that it is drinkable and healthy.
Tissue engineering
In the tissue engineering, nanofibres are used to produce scaffolds that support the growth, multiplication and reproduction of the biological tissue to be replaced. They are most often used to cover and heal burns and to control the release and transport of drugs into damaged tissue.
The inherent biodegradability of the scaffold allows tissue transplantation and healing without the need for surgical removal of the nanofibre scaffolding.
Photovoltaics and the automotive industry
In the power industry, choosing the right polymer allows electrons or ions to be conducted, making nanofibres interesting for energy production and storage. In this area, nanofibres can be used for photovoltaic panels, battery storage systems and capacitors.
The application of nanofibres to rechargeable batteries using silicon properties is currently being considered. This would improve the efficiency of lithium batteries present in plug‑in electric vehicles. Nanofibres are already used in the automotive industry to produce more efficient automotive filters.
Military technology
In the military, nanofibres are used to improve the ability to detect chemical and biological agents. Nanofibre‑enriched garments improve the protection of military personnel through their ability to filter and decompose toxins.
This particular area of application has given rise to self‑cleaning personal protection equipment. These mainly include masks composed of two "layers." The first is used to filter the air, while the second contains activated carbon, which absorbs harmful gases and impurities.
We are currently working on the development of such an effective nanofibre, which will replace the activated carbon layer and thus improve the permeability of the fabric and the comfort of the end user. In addition, nanofibres are able to capture even small particles such as viruses.
Sensors and meters
The remarkable properties of electrospun nanofibres (such as large surface area, porosity, flexibility and relatively low cost) make them an excellent choice for sensor applications.
They are used, for example, in sensors that monitor biological parameters, such as glucose values, up to gas monitoring systems. As part of the protection of soldiers, nanofibre sensors are newly installed in the masks, which alert the wearer when the amount of harmful gas is above the limit and life threatening.
Textile industry
Nanofibres have also found application in leisure functional clothing. Nanofibre microporous membranes have the potential to provide the wearer with thermal comfort, a better level of water resistance, and, at the same time, efficiently dissipate vapours.
What else are nanofibres used for?
- Composite reinforcements,
- Non‑woven fabrics,
- Liquid crystal optical devices,
- Cosmetics,
- Protective clothing,
- Oil and water separation filters.
It should be borne in mind that many of these applications are still in the research and testing phase.
Resources
- https://filti.com/what‑is-nanofiber/,
- https://link.springer.com/referenceworkentry/10.1007/978‑3-319‑42789-8_54‑1,
- https://www.linarinanotech.com/blogs/learn/what‑are-nanofibers‑used-for,
https://www.technickytydenik.cz/rubriky/archiv/nanovlakna‑vcera-dnes‑a-v‑budoucnu_13910.html.https://en.wikipedia.org/wiki/Electrospinning.