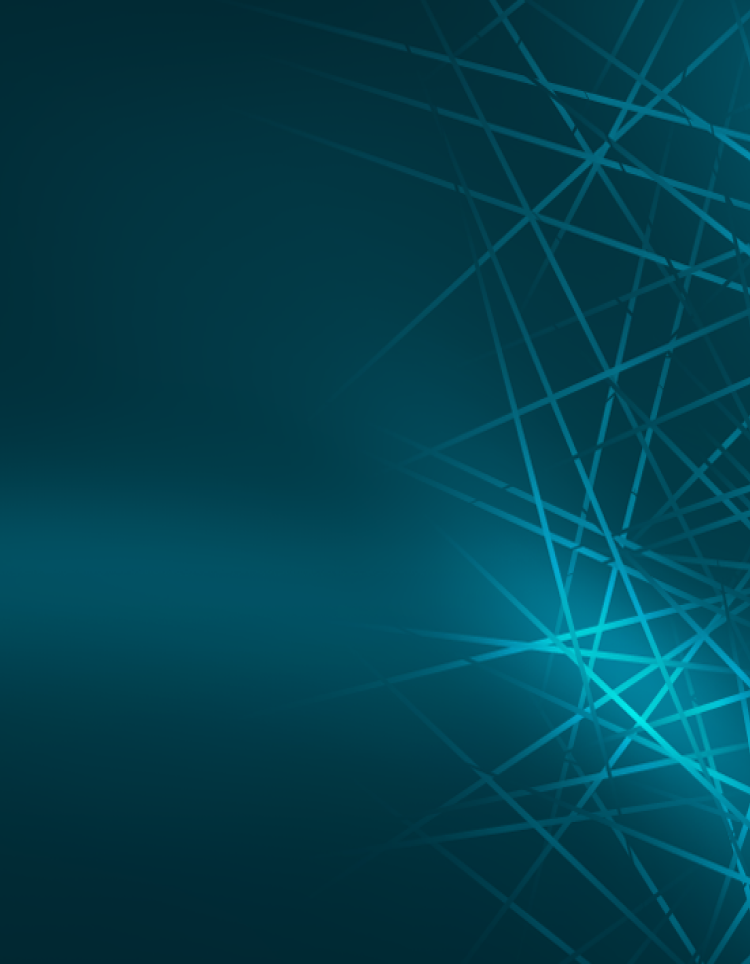
LINEA line. Nanofibers production for various types of applications.
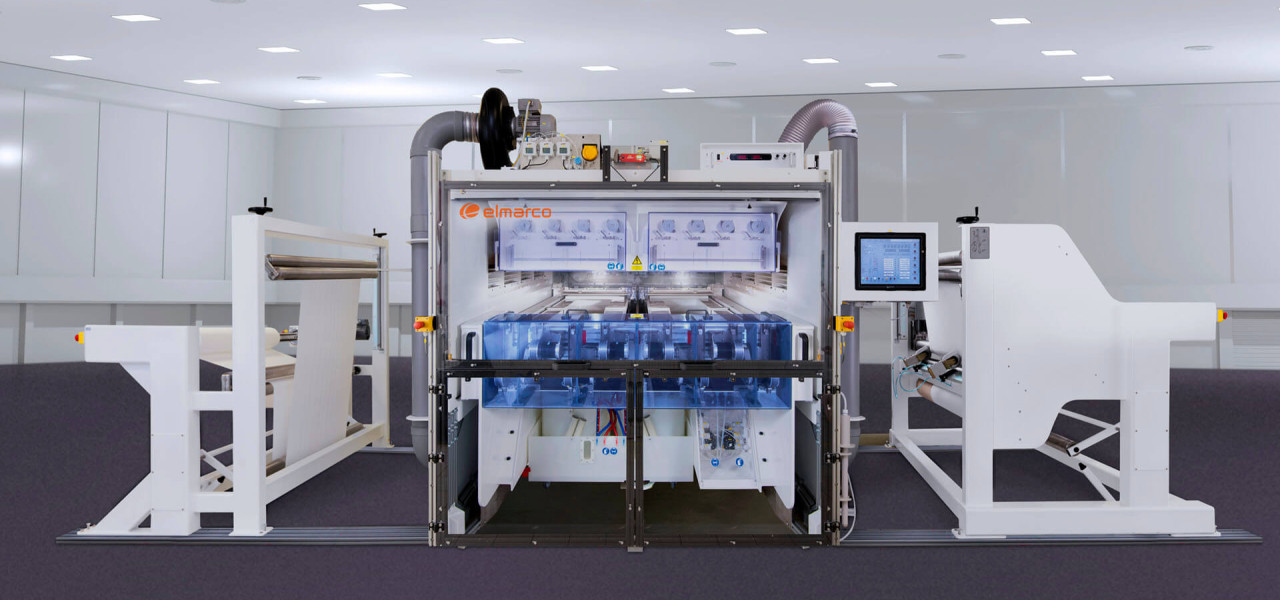
Nanospider™ technology uses a thin stainless steel wire as the spinning electrode and a moving head to apply the polymer solution along the entire length of this wire. When a strong electrical field is applied, nanofibers are formed from the thin polymer layer on the spinning electrode. Only a small amount of polymer solution is applied to the wire during each cycle of the moving head which is a prerequisite for maintaining consistent nanofiber morphology during long‑term production.
This technology forms nanofibers along the entire length of the spinning wire which is the key to industrial scale production.
LINEA line application
The magic is in the technology
The technology uses a stationary spinning electrode wire where the polymer solution is applied to the wire using a special moving head with a calibrated orifice. This applies a thin layer of polymer solution to the surface of the wire. When high voltage is applied, the surface tension of the polymer solution is overcome by the electrostatic force and the solution is forced to move to an area with a lower electrical potential which starts the formation of the Taylor cones. As the liquid stream moves towards the collecting electrode, the solvent evaporates, the nanofibers are stretched, and subsequently deposited on the substrate material which sits below the collecting electrode.
More electrodes for higher productivity
The equipment is modular and production capacity can be increased by adding up to four units in series. Production throughput increases linearly with each additional unit.
Technological benefits
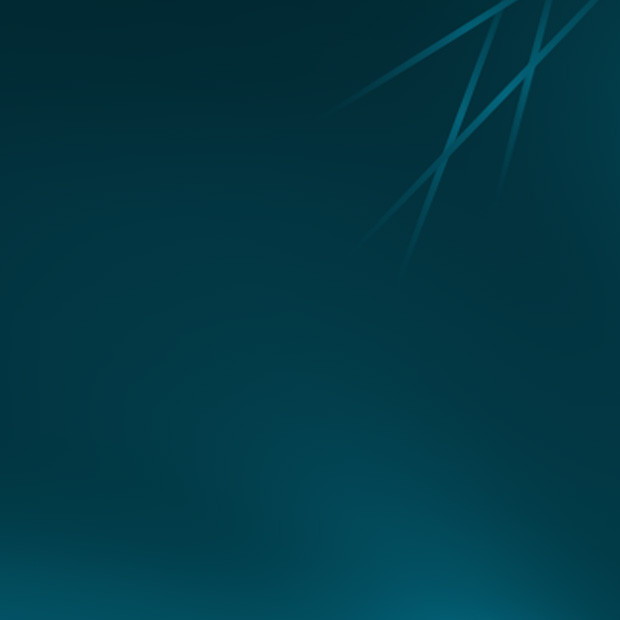
High throughput
and uniformity
NS 8S1600U example: 20,000,000 m² coated material per year for PA6, fiber diameter 150 nm, basis weight 0.03 g/m³, 85% serviceability
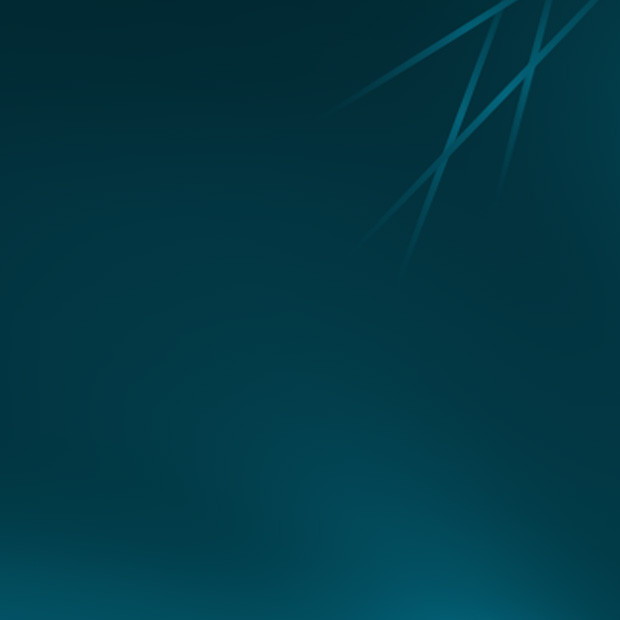
Cost‑effective
production
The device allows for optimization of the process for specific polymer, substrate and product parameters.
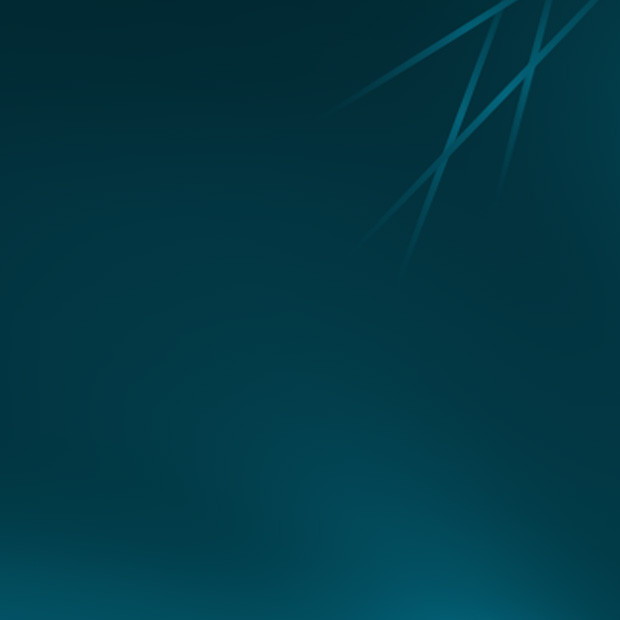
Production scalability
Each unit contains 8 spinning electrodes. To increase productivity, up to 4 electrospinning units with a total number of 32 spinning electrodes can be included in one production line.
LINEA technology use in practice
LINEA line products
Scalable industrial production line
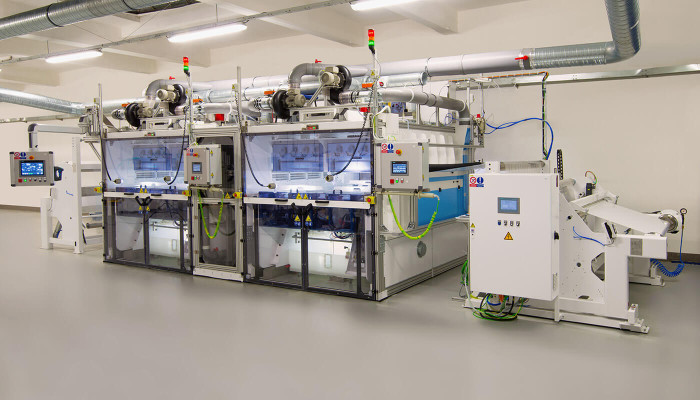
Nanospider™ NS 8S1600U
Nanospider™ NS 8S1600U is our most versatile module for high‑volume nanofiber production. It is designed for ease of use, scalability, and flexibility in the production of the highest quality nanofibers. The 1.6 meter wide electrospinning units are modular, allowing up to four NS 8S1600U units to be combined into one production line, which results in the capacity to produce tens of millions of square meters of nanofiber materials annually.
Technical specifications of the NS 8S1600U production line
Number of electrospinning units | 1 |
---|---|
Number of application modules | 2 |
Modules can also be operated independently with different polymers | |
Total number of spinning electrodess | 8 (4 per module) |
Spinning electrode width (adjustable width 1000‑1600 mm) | 1600 mm |
Electrospinning voltage | 0–140 kV |
Unwinding speed (depending on the desired nanofiber layer) | 0,2–40,0 m/min. |
Distance of the spinning electrode to the substrate | 150–250 mm |
The distance of the wires of the collecting electrode above the substrate | 30–130 mm |
Electrical Consumption | 5 kW |
Machine dimensions
|
Height 2930 mm |
Width 3200 mm | |
Length 2600 mm | |
Weight 2500 kg |
Temperature | 20–30 °C |
---|---|
Humidity | 20–40 % RH |
Hours of operation | 24/7 operation |
Startup time | Typically within 20 min. |
Time required to fill the polymer | 15 minutes |
Tank volume | 60 litres (2×30 litres) |
Monthly maintenance allowance | Approximately 15 hours (depends on the process) |
Serving staff | 1.5 person/shift |
---|---|
Production premises requirements | Approximately 200 m² (10×20 m) |
Minimum ceiling height of 4 m | |
A space with little dust is required | |
Other special requirements | Appropriate exhaust air treatment |
Dry compressed air | |
Inert gas | |
Ventilation requirementsVentilation requirements | Typically 2500 m³/h ‑ for production line + peripherals (for line with one spinning unit) |
Easy transition from laboratory scale to industrial production
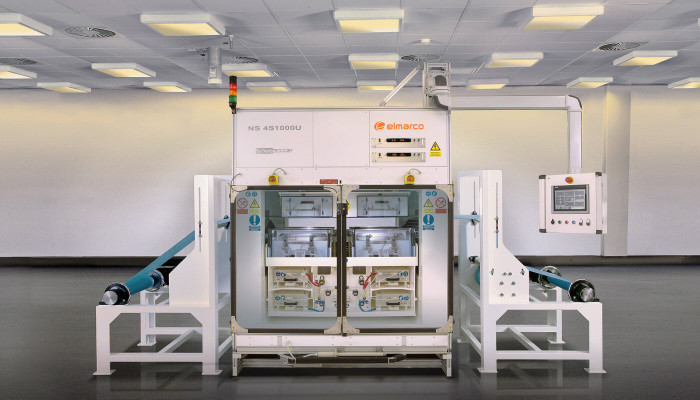
Nanospider™ NS 4S1000U
Nanospider™ NS 4S1000U enables the production of roll‑to-roll nanofibers on a semi‑industrial scale. The line is capable of producing a nanofiber layer 1000 mm wide and can be supplemented with external peripherals. It is an ideal solution for those who are ready to scale up their process from a laboratory concept to moderate volume production, to fine tune the entire production process, and to seed the market. The NS 4S1000U is also ideal as a production line for high value nanofiber materials that have lower annual volume requirements.
Technical specifications of the NS 4S1000U production line
Number of electrospinning units | 1 |
---|---|
Number of application modules | 2 |
Modules can also be operated independently with different polymers | |
Total number of spinning electrodes | 4 (2 per module) |
Spinning electrode width (adjustable width 300‑1000 mm) | 1000 mm |
Electrospinning voltage | 0–140 kV |
Unwinding speed (depending on desired nanofiber layer) | 0,2–12,0 m/min. |
Distance from the electrode to the substrate | 150–250 mm |
Electrical Consumption | 6 kW |
Machine dimensions | Height 2450 mm |
Width 2300 mm | |
Length 2100 mm | |
Weight 1500 kg |
Temperature | 20–30 °C |
---|---|
Humidity | 20–40 % RH |
Hours of operation | 24/7 operation |
Startup time | Typically within 20 min. |
The time required to fill the polymer | 10 minutes |
Tank volume | 20 litres |
Monthly maintenance allowance | Approximately 15 hours (depends on the process) |
Serving staff | 1 person/shift |
---|---|
Production premises requirements | Approximately 100 m² (10×10 m) |
Minimum ceiling height of 4 m | |
A space with little dust is required | |
Other special requirements | Appropriate exhaust air treatment |
Dry compressed air | |
Inert gas | |
Ventilation requirements | Typically 2000 m³/h ‑ for production line + peripherals (for line with one spinning unit) |
Necessary peripherals for NS 8S1600U and NS 4S1000U lines
NS 3S500U - equipment for research and small‑volume production
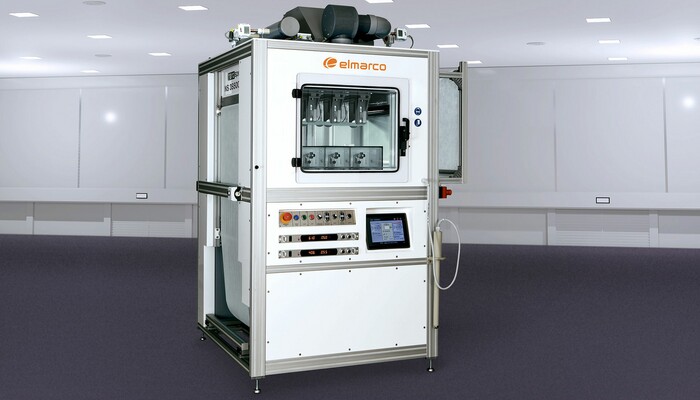
The NS 3S500U electrospinning machine is a versatile tool for the research and development of nanofiber products, as well as for small‑scale production. It combines the features of a high‑end laboratory instrument with the possibility of industrial production.
Flexibility of used polymers and substrate materials
The NS 3S500U device allows electrospinning a wide range of polymers, including highly viscous polymer solutions. These can be spun onto many types of base material including cellulose, synthetic materials or fiberglass.
Nanospider™ needle‑free technology enables easy process optimization. Adjustment of most process specifications is possible using the touch screen.Quality and safety
- Made from FDA certified materials
- Meets all CE requirements
- Security door locks
- Safety switches
- Integrated substrate material rewinding
NS 3S500U functions and recommended use
The device is equipped with a peristaltic pump for continuous filling, with the ability to constantly mix the solution. This allows for an automated operating mode, and the device is also suitable for small‑volume production of nanofibrous materials.
- The fastest upscale for industrial production
- The material produced has high performance/yield and uniformity compared to needle technologies
- 500 mm wide layer of nanofibers
- Allows control of all process parameters (voltage, substrate speed, die size, application head speed, wire distance from the substrate, and others)
- Continuous operation up to 8 hours (depending on the polymer solution and device setting)
Expanded research and production capabilities thanks to additional types of electrodes
In addition to the standard wire electrode, each NS 3S500U machine is equipped with two additional types of collecting electrodes - a rotating electrode and an endless belt. These can be variably changed according to your needs, significantly expanding the possibilities of work on the NS 3S500U machine.
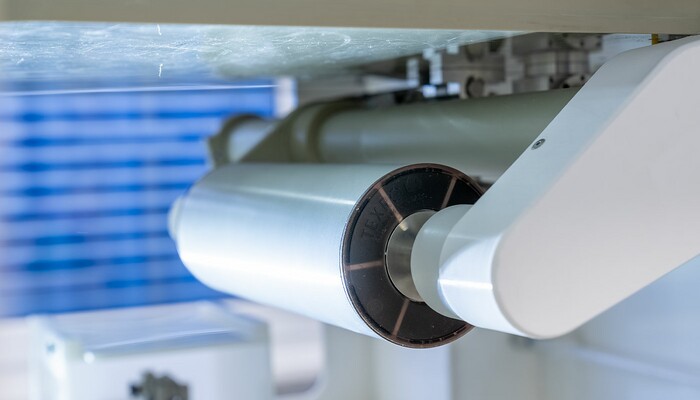
Rotating electrode
The rotating electrode allows a wider utilisation of the NS 3S500U machine. The wire collecting electrode is replaced with a cylindrical electrode. Due to the built-in drive it is possible to spin individual collectors to speeds of up to 2000 RPM, which, depending on the collector diameter, allows to achieve the peripheral speed of up to 10 m/s. This type of collecting electrode is recommended for preparation of samples with oriented fibres or materials comprising successively overlapping nanofiber layers.
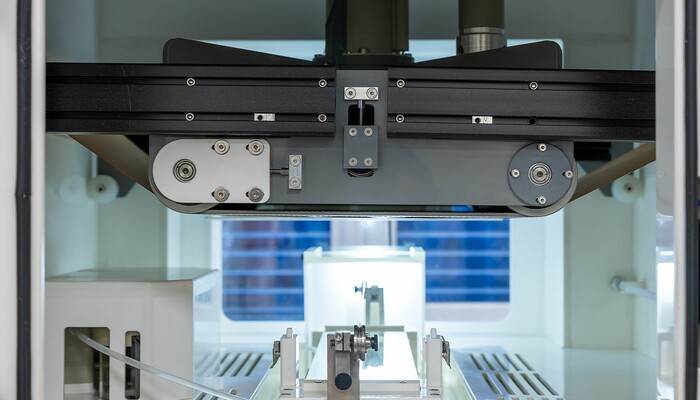
Endless belt
As a collecting electrode, the endless belt enables electrospinning on substrate materials with a wider range of volume resistance (1010 – 1016 Ohm) that cannot be used with the standard wire collecting electrode. The substrate layer is fastened to the belt using electrostatic force, which significantly improves the mechanical support of the substrate material. Thanks to the electric motor, the belt moves at the same speed as the substrate material so there is no undesirable stress. In addition, the standard belt can be replaced with a PTFE version, which can be operated without substrate and used for direct spinning thanks to its drive.
NS 3S500U technical specifications
Stationary electrode string system | |
---|---|
Number of spinning electrodes | 3 |
Spinning electrode width | 500 mm |
Integrated one‑way substrate material unwinding/rewinding | |
Electrospinning tension | 0‑100 kV |
Unwinding speed | 5‑5000 mm/min. |
Electrode distance from the substrate | 120‑240 mm |
Effective width of the nanofibrous layer | 300‑500 mm |
Continuous solution pumping (depending on polymer/solvent solution) | up to 8 hours |
Operation time in batch mode (depending on polymer/solvent solution) | up to 60 min. |
Consumption | |
Power consumption (up to 5.4 kW when external winding is connected) | up to 1,4 kW |
Dimensions | |
Height | 2250 mm |
Spinning electrode width | 1640 mm |
Length | 1470 mm |
Weight | 510 kg |
The stated dimensions are without peripherals, incl. additional aluminum frame
Accessories | ||
---|---|---|
Solution containers | ||
Production mode | Type of trays | Volume |
Continuous pumping | Peristaltic | 1 000 ml |
Batch mode | Standard | 50 ml x 2 |
Batch mode | Small | 10 ml x 3 |
Optional collecting electrode | ||
Rotating electrode | Endless belt | |
RPM: up to 2000 | Speed: 5-5000 mm/min | |
Cylindrical collectors | Collectors: PU, PTFE | |
Peripheral speed: up to 10 m/s | ||
Additional aluminum frame for easy sample collection | ||
Integrated fire extinguishing system | ||
Optional peripherals | ||
(NS AC 150) Air conditioning unit | ||
External base material unwinding and rewinding |
Throughput | Depends on the polymer, substrate, process and fiber diameter |
---|---|
Effective nanofiber layer width | 300‑500 mm |
Operating temperature | 20‑30 ºC |
Working humidity | 20‑40 % RH |
Process air flow | 30‑250 m3/hour |
Serving staff | 1 person |
---|---|
Production premises (when connecting external winding 4x6 m) | 4×4 m |
Extraction ventilation connection required | |
Power (adapted for networks in all countries) | 230 V |
Power supply (external winding) | 3×400 V |
Exhaust ventilation | 250 m³/hour |
Compressed air (for external winding only) | 5 bars |
Appropriate exhaust air cleaning required | |
Supply air connection for optional AC unit | |
Fire extinguishing system connection | |
External grounding |
Background | |
---|---|
Maximum width of the substrate roll | 550 mm |
Max. roll diameter (with external winding 500 mm) | 400 mm |
Possible substrate materials | Cellulose, synthetics, fibreglass, films |
Polymers | |
Versatile setup for soluble polymers | |
Thread specifications | |
Adjustable fibre diameters | approx 80‑700 nm |
Fibre diameter deviation | typically +/- 30 % |
Homogeneity of the transverse profile and winding direction | typically +/- 5 % |
All fiber specifications are polymer, substrate and process dependent |
Optional peripherals for NS 3S500U
Contact us
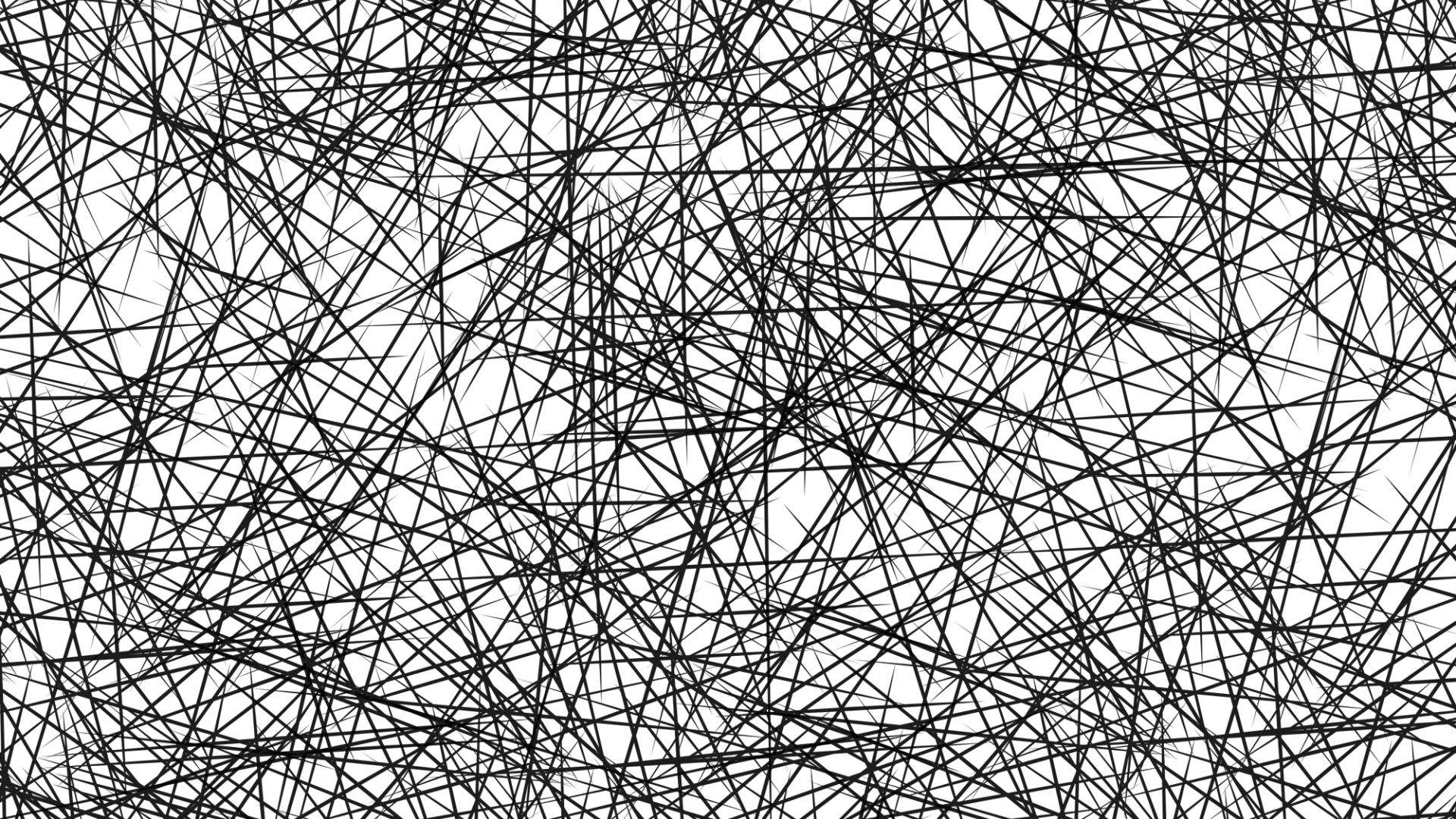