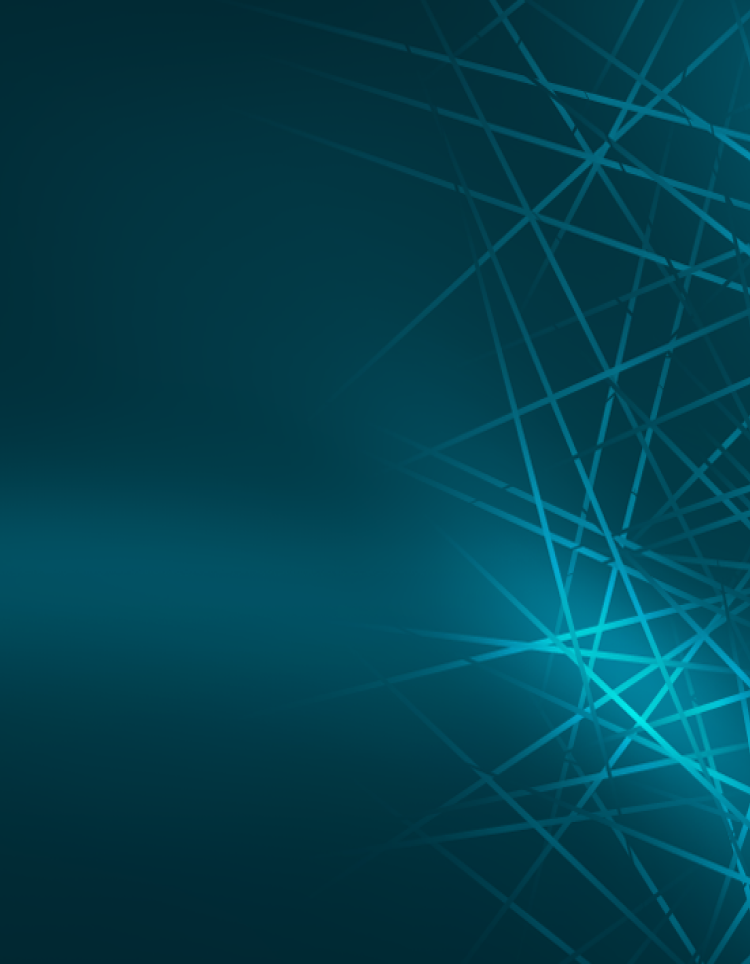
INFINITY line. Solutions for advanced membranes.
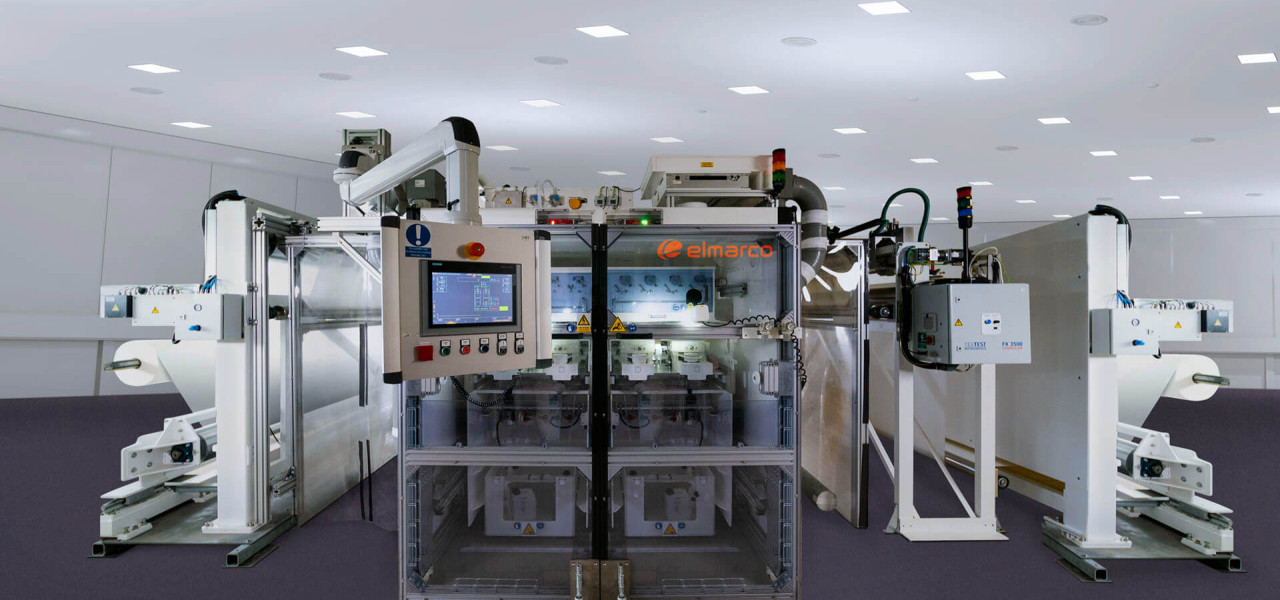
Minimization of defects
The INFINITY line produces virtually defect‑free nanofiber membranes for use in very demanding applications. It uses the Nanospider™ needle‑free principle, but the nanofiber jets are not interrupted thanks to the continuous movement of the electrospinning wire.
INFINITY line application
Technological details
Nanospider™ technology uses a spinning electrode in the shape of a thin wire which is continuously coated with polymer solution.
Under the influence of a strong electrical field, nanofibers are then formed from a thin polymer layer on the electrode.
Nanospider™ technology uses a spinning electrode in the shape of a thin wire which is continuously coated with polymer solution. Under the influence of a strong electrical field, nanofibers are then formed from a thin polymer layer on the electrode.
The high‑voltage field acts between two electrode wires: spinning and collecting.
- The spinning electrode wire is connected to a positively charged high‑voltage power source
- The collecting electrode wire is connected to a negatively charged high‑voltage power source
The filament electrode consists of a wire in a loop. The polymer solution is continuously applied to the wire using a static coating device. By applying a high‑voltage field, the surface tension of the polymer solution is overcome by the electrostatic force and the nanofiber jet is formed. As the nanofiber jet travels towards the collecting electrode, the solvent evaporates and the fiber is stretched. The nanofiber is deposited onto the substrate which is below the collecting electrode.
Technological benefits
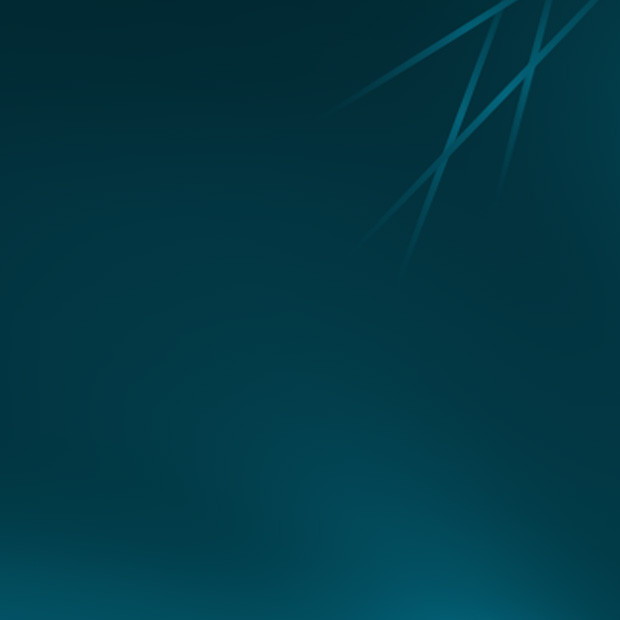
Minimal defects
This innovation enables production of high‑performance nanofiber membranes for use in HEPA filtration, liquid filtration, fuel cells, and battery separators.
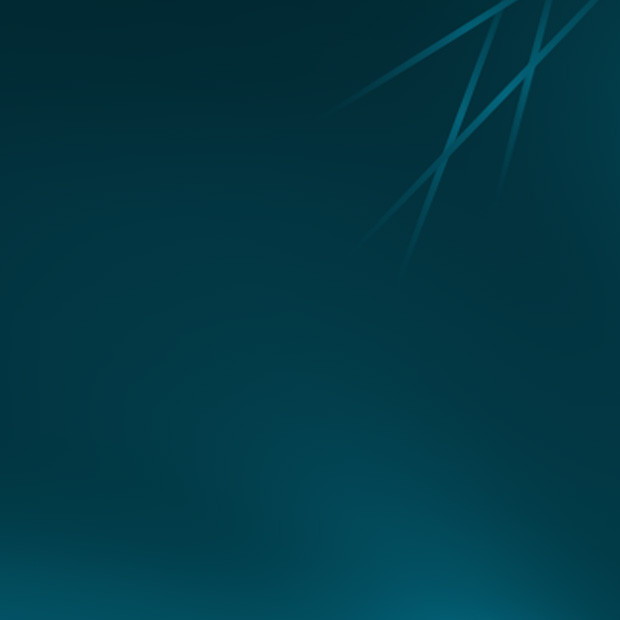
Production scalability
Each INFINITY unit contains four wire loops which creates eight spinning electrode zones. Up to four units can be combined in series to increase the productivity of the line.
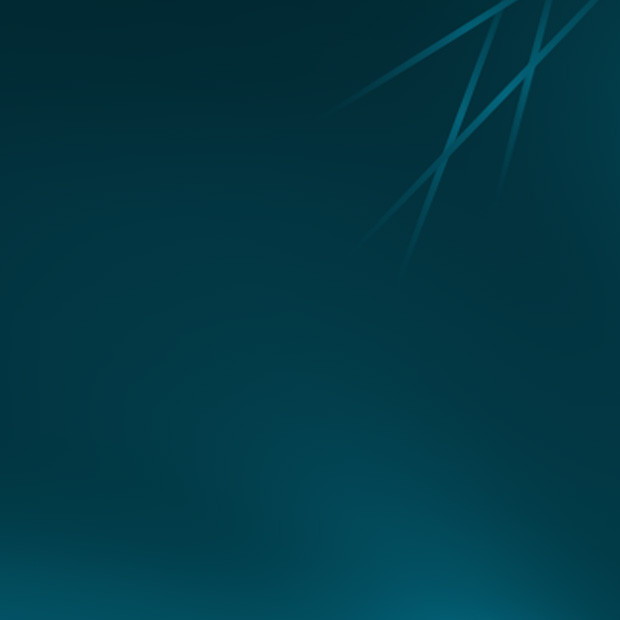
Consistent production
The environment inside the INFINITY line chamber is closely regulated for airflow, temperature, and humidity as these are key elements of stable, long‑term production of defect free nanofibers. Each chamber is designed to maintain this environment for consistent industrial production of nanofiber materials.
INFINITY technology in practice
INFINITY line technical specifications
Number of electrospinning units | 1 |
---|---|
Number of rotating modules | 2 |
Modules can also be operated independently with different polymers | |
Total number of electrospinning electrodes | 8 (4 per module) |
Spinning electrode width | 1,600 mm |
Electrospinning voltage | 0‑140 kV |
Unwinding speed (depending on the desired nanofiber layer) | 0.01‑5 m/min. |
Rotating wire speed | 0‑10 m/s |
Distance from the electrode to the substrate | 150‑250 mm |
Electrical consumption | 5‑10 kW |
Machine dimensions | Length 13,800 mm |
Width 9600 mm |
Temperature | Specific to the polymer used in the process (example PA6 on cellulose - temperature varies between 20‑30°C) |
---|---|
Humidity | Specific to the polymer used in the process (example PA6 on cellulose - humidity is 20‑40% RH) |
Hours of operation | 24/7 operation (tanks require changing every 16‑24 hours) |
Startup time | Typically within 20 min. |
Time required to fill the polymer | 20 min. |
Tank volume | 60 l (2×30 litres) |
Time required to produce one batch | Maximum 24 hours, typically 16 hours. |
Monthly maintenance allowance | Uptime around 85‑89% |
Serving staff | 1 person/shift |
---|---|
Production premises requirements | Approximately 200 m² (10×20 m) |
Minimum ceiling height of 4 m | |
Flat and solid surface with a 500 kg/m² load capacity. For ease of operation, the floor must be sufficiently level. | |
Other special requirements | Internet connection ‑ remote access service. |
IDry compressed air: 6‑8 bar, can vary within 200 Nl/min. up to 2000 Nl/min. according to settings and operating mode. | |
Inert gas: 0.5 bar, can vary within 2 Nl/min. up to 200 Nl/min. for different times in operating mode. | |
Ventilation requirements | Typically 2000 m³/h - for production line + peripherals (for lines with one electrospinning unit) |
Necessary peripherals
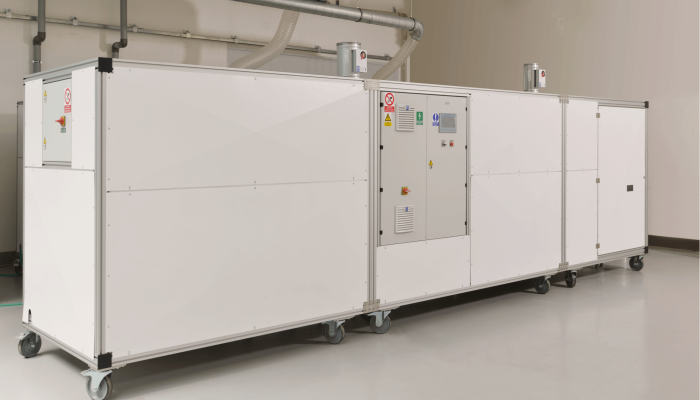
Precise air conditioning
The atmosphere within the electrospinning chamber is one of the most important factors that affects fiber morphology and process performance. For most polymer solution formulations, the target relative humidity is in the range of 20‑50%, with a temperature range between 18‑30°C. The air conditioning unit is designed to ensure precise regulation of temperature and relative air humidity inside the electrospinning unit.
MORE ABOUT AIR CONDITIONERS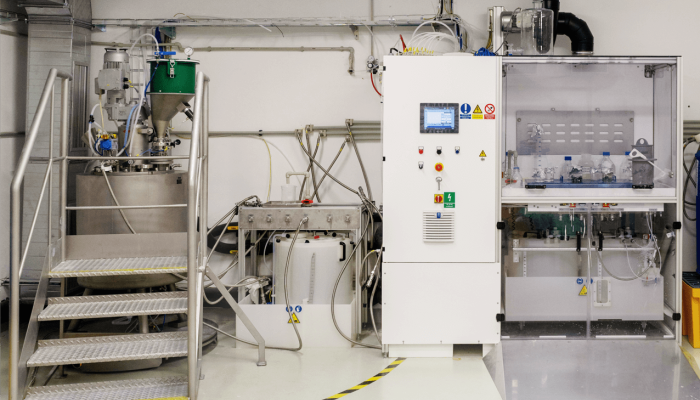
Polymer Preparation System Compact
Polymer solutions for use in the electrospinning unit are prepared in the PPSC. The stainless steel mixing vessel has an integrated water circulation system that heats and cools the polymer solution during preparation. The entire process of preparing the polymer solution is designed to minimize operator intervention and the operator is not exposed to the solvents or polymer solution because a closed system is utilized.
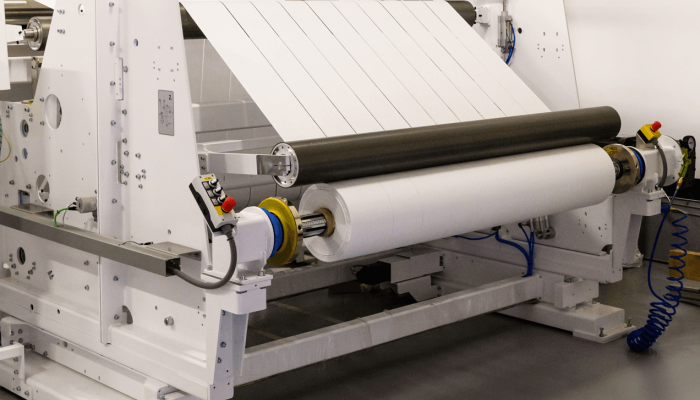
Unwinding and rewinding
The unwinder and rewinder consists of steel frames with precision motors driving shafts holding the uncoated and nanofiber coated substrate rolls. We partner with external suppliers to provide this equipment, including safety fencing, based on our specific requirements for nanofiber production.
Support tent
The tents contain a system of rollers which support and prevent deformation of the substrate material. The tents also minimize the mixing of the atmosphere inside and outside the chamber to help ensure stable conditions for electrospinning.
Data storage and remote access
The data storage system records critical process data and machine settings which are used as production records. The data can be accessed via a local network connection. The system is also configured with a private and secure VPN which can be accessed for remote diagnostics and service requests.
Waste air treatment
Since the electrospinning process involves the use of solvents, the resulting emissions must be treated to minimize air pollution and we can provide this hardware through third‑party vendors. The specific concentrations and flow rates depend on the machine settings which are specific for every product. Through third‑party vendors, we can provide the appropriate hardware to eliminate the harmful emissions.
Contact us
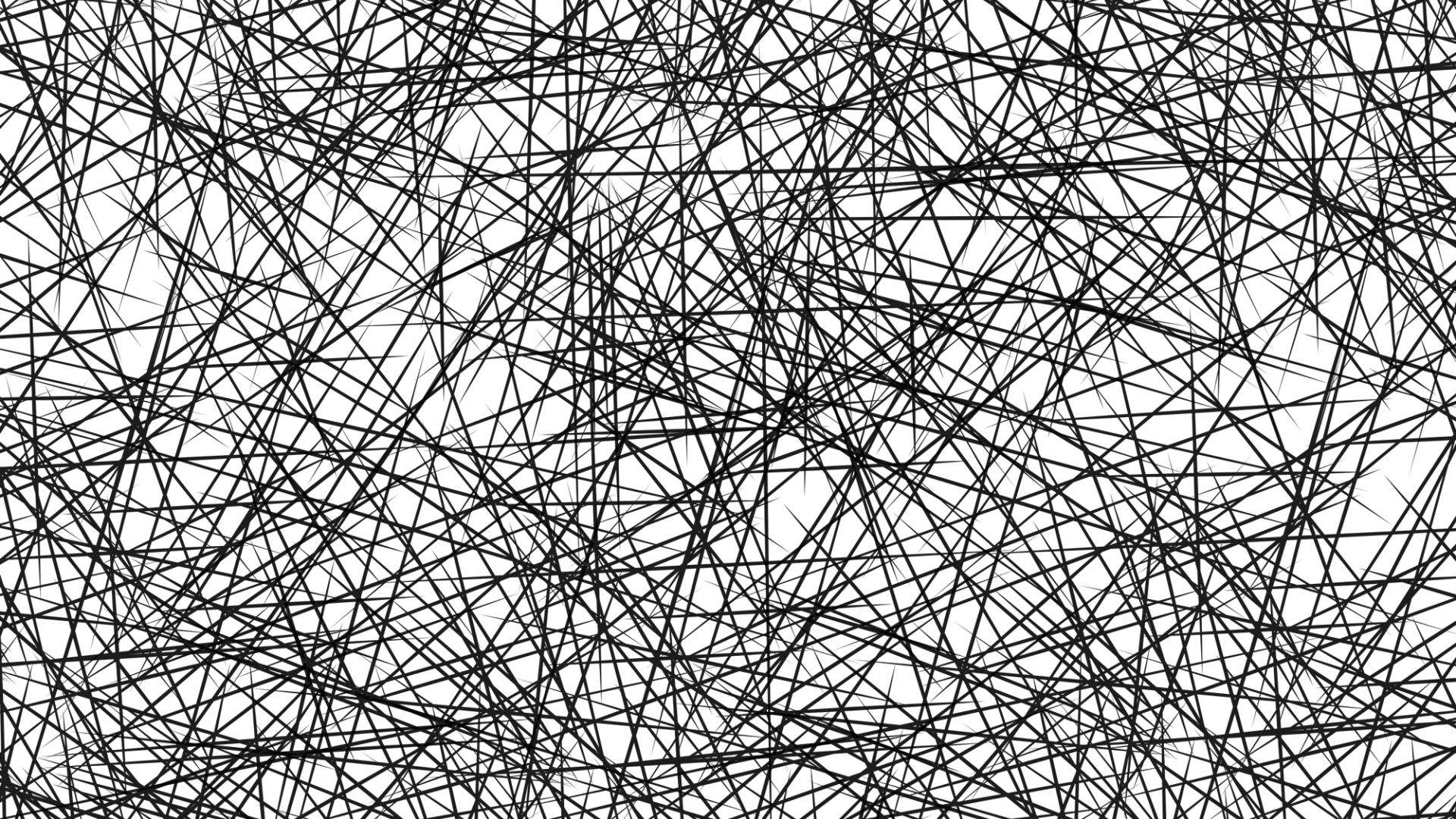