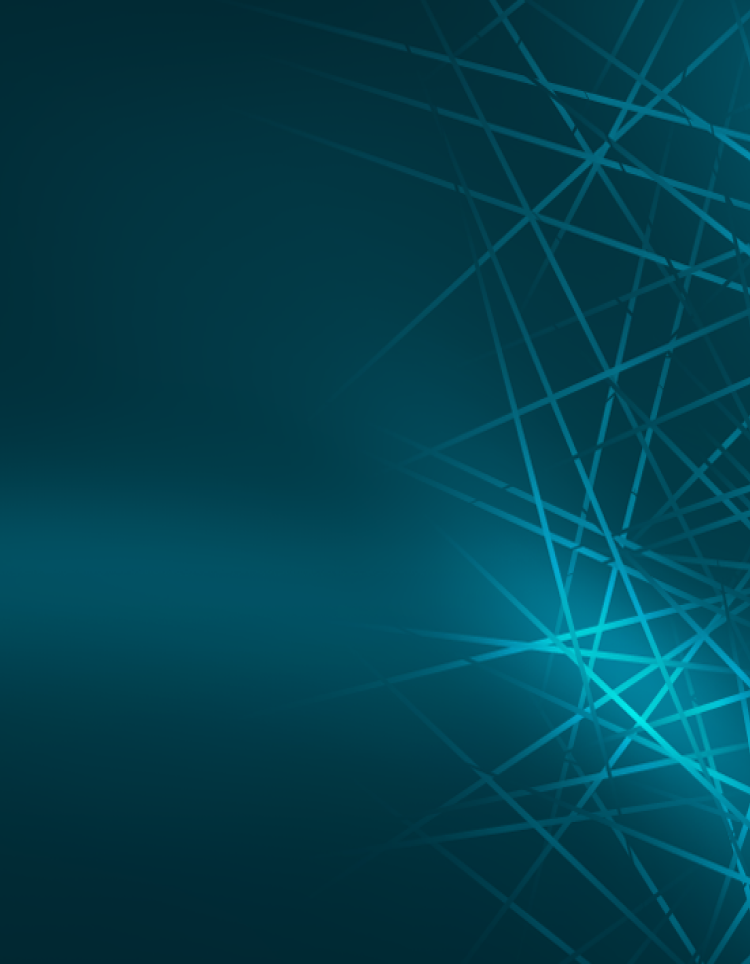
Hope for third world countries – water filtration through nanofibres and the ability to drink without fear!
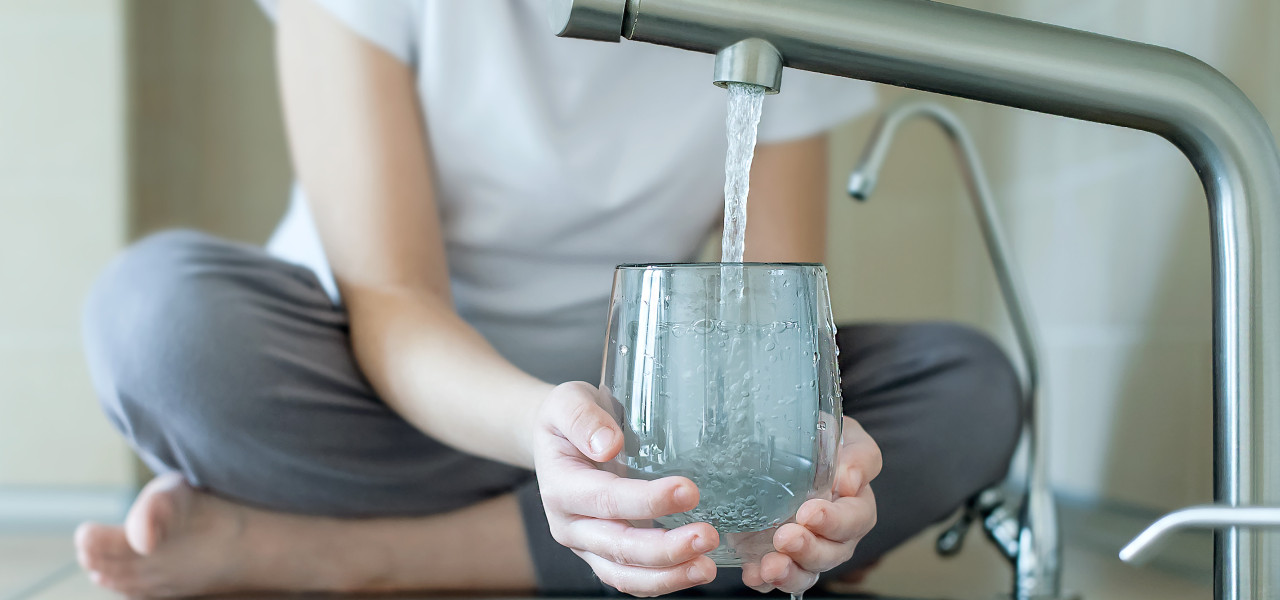
One tenth of the world’s population has problems with drinking water! More than 771 million people on the planet do not have access to clean drinking water, and water contamination by viruses and bacteria is a major cause of disease in developing countries.
Currently, aggressive chlorine‑based disinfectants or membrane microfilters are most commonly used to keep the microbial population in water under control and to purify the water. However, the reliability of these methods is questionable.
The use of disinfectants leads to the formation of harmful disinfection by‑products and the growth of resistant pathogens that are immune to chlorination.
In the case of membrane microfiltration, a major drawback is the potential for biofouling and rapid clogging of the filter. There is also the penetration of viruses, which are not captured by the micro‑membrane, further into the water.
Not to mention the fact that the lifetime of the membrane decreases, its permeability increases rapidly, and the cleaning costs increase with every successive round of filtration. The solution? Make a filter, through which the contaminated water is run in a flash. It purifies it so well that it is instantly drinkable, and most importantly, safe for health. Only a filter made of nanofibres meets all these conditions.
Nanofibres catch even the smallest virus particles!
Why are nanofibre filter systems so promising? The most important benefits are the low weight of the filter and its high permeability for water flow and small pore size. This predisposes them to trap harmful particles smaller than 0.3 micrometres!
Another major positive of nanofibre filters is their variety. Filter media can vary in thickness, fibre diameter and distribution, porosity, and permeability. It all depends on the spinning method and the polymer chosen.
Interesting Fact: Newly added to nanofilters are so‑called nanobiocides, which tend to be e.g. metal nanoparticles, antibiotics, and bacterial agents. These are added directly to the polymer solution and make the filter manufacturing process more efficient. They allow, for example, the production of nanofibres with a modified surface in one step, i.e. without post‑production modifications. The result is an extra‑fine nanofibre mesh that does not let in the slightest pathogen and is very fast to make.
Several methods are used to produce nanofibres for water purification filters (= preparation of clean drinking water). One of the most reliable is electrospinning.
Electrospinning – antimicrobial coating or a self‑functioning membrane!
Electrospinning is a simple, fast, and effective method of nanofibre formation involving only three components, namely a high voltage source and spinning and collection electrodes.
The filtration membrane made of nanofibres picks up bacteria and virus colonies from the water and does not cause any biological pollution. Thanks to this method, the membrane has an extended lifetime and lower energy consumption. It also allows chemicals‑free cleaning and produces no disinfection by‑products.
The nanofibres show potential either as an antibacterial layer on the filter or as a self‑supporting membrane. They have a much higher surface area and volume than conventional melt‑blown microfibres, ensuring effective separation of even the smallest particles.
Free-surface spinning with the NanospiderTM technology – industrial production without the use of spinning nozzles!
Elmarco, a leading supplier of industrial scale nanofibre production equipment, offers a portfolio of Nanospider™ machines on the market ranging from laboratory sample preparation to high volume industrial production. This innovative technology of spinning from the free surface of the polymer solution in a strong electrostatic field enables spinning from the entire solution surface without the use of nozzles.
What makes this method so groundbreaking? In particular, the quantity. After its introduction, Elmarco was able to start producing nanofibres on an industrial scale, taking advantage of the flexibility to set parameters according to the product’s needs. Input resources can be freely varied and the versatility of the technology allows a plethora of different nanofibre materials to be produced, including extra efficient liquid filters.
Key benefits of using the NanospiderTM method to produce filtration membranes:
- High production capacity and scalability,
- Cost‑effective industrial production and easy maintenance,
- Flexibility of input polymers and substrate materials,
- Unprecedented precision in filter “geometry” associated with uniform nanofibre diameter,
- Ability to add carbon particles and other additives to the process for more efficient and selective water filtration,
- High strength and permeability – water flows quickly through the filter and the filtration process is, therefore, not delayed by anything.
Among other things, nanofibre filters are lightweight, small, and durable, so they are easy to transport anywhere in the world, including the aforementioned third world countries. People in these countries can easily access drinking water without fear of contamination.
Sources used:
- Botes, M., & Eugene Cloete, T. (2010). The potential of nanofibers and nanobiocides in water purification. Critical reviews in microbiology, 36(1), 68‑81.
- Lukas, D., Sarkar, A., & Pokorny, P. (2008). Self‑organization of jets in electrospinning from free liquid surface: A generalized approach. Journal of Applied Physics, 103(8), 084309.
- Mikeš, P., Baker, D. A., Uhlin, A., Lukáš, D., Kuželová-Košťáková, E., Vidrich, A., ... & Tomani, P. (2021). The mass production of lignin fibres by means of needleless electrospinning. Journal of Polymers and the Environment, 29(7), 2164‑2173.
- https://www.dailymail.co.uk/sciencetech/article‑6084259/The‑nanofiber-net‑capture-clean‑drinking-water‑air.html.