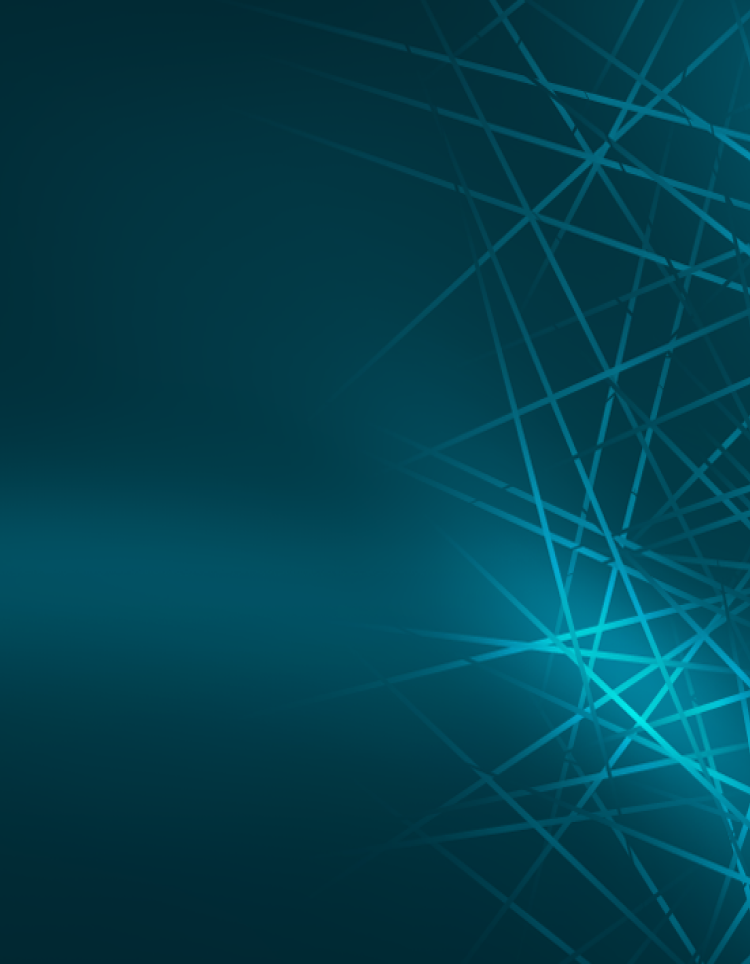
Nanofiber-Coated Fabric vs. Conventional Fabric: Thin Membrane Is Enough to Protect from Chemicals or Airborne Pollutants!
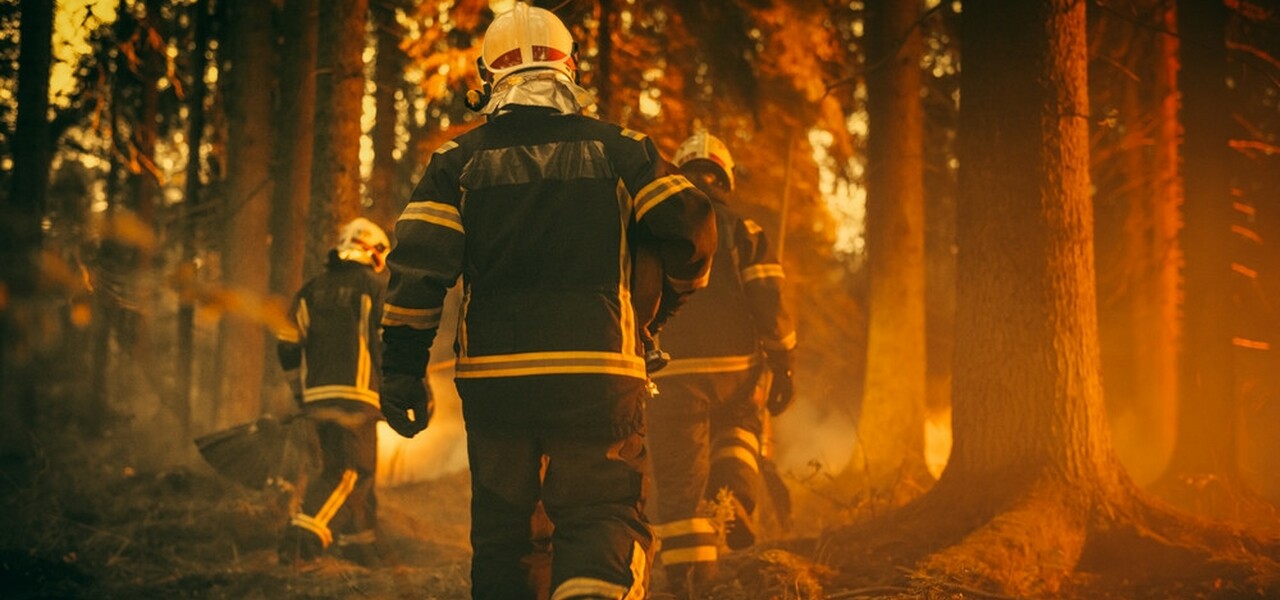
Imagine being able to add extra thin nanofibres to clothing fabrics to basically make them behave the way you want and need them to. Exciting idea? Of course. And that is why nanofibre‑coated fabrics now have a clear advantage over any conventional fabric.
That nanofibres are the technology of the future is already known not only by interested researchers and visionary companies, but also by us, ordinary people. Now is the time to prove to everyone that nanofibres can take the clothing industry to a whole new level and be part of the so‑called fabrics of the future. What are the benefits of a nanofibre‑coated garment compared to a one made of conventional fabric?
Impermeability to Harmful Particles from the Air
The presence of micro and nanoparticles in the air due to air contamination is one of the biggest environmental risks to human health. Both short‑term and long‑term exposure to these molecules has a serious impact on human health. It is, therefore, necessary to develop protective clothing and ensure that exposure to these particles is as low as possible. A typical example is the protective clothing worn by firefighters who work in environments with higher concentrations of harmful particles in the air on an almost daily basis.
Conventional fabric based on air filtration relies on the use of micron glass fibres implemented in the fabric. However, these will only filter out particles of micron size and larger. They do not have the capacity or the right pore size to capture sub‑microns. Only nanofibrous textiles, thanks to their ultrafine structure, large surface area‑to-volume ratio, and corresponding porosity, can ensure impermeability of even the smallest nanoparticles.
Water Resistance and Water Vapour Venting
Protective outdoor clothing should meet three principles according to the wearers – it should be waterproof, breathable, and provide thermal comfort. This ensures the wearers’ comfort in extreme weather conditions and protects them from rain, snow, and wind.
The nanofibre material allows for two seemingly incompatible realities.
On the one hand, it will limit the penetration of liquid water inside, and on the other, it will allow water vapour to escape outside. Thus, the wearer of this garment will not get wet (e.g. in rain or snow) and, at the same time, will not be uncomfortably sweaty and overheated because the nanofibre membrane lets the accumulated moisture out.
Conventional waterproof materials are rarely breathable. Techniques such as biaxial stretching or phase separation have been used in the past, but with limited success. The resulting fabric was unbreathable, heavy, and the wearer would quickly sweat in it, which was very uncomfortable as moisture had no way to escape.
When the researchers focused on using electrospinning to produce a waterproof and breathable material, they found that they were able to produce membranes that were both dense and had interconnected pores. The presence of micro- and nanometre‑sized pores allows for moisture transport and limits the penetration of water and wind. However, it is reported that fabric made by spinning only shows good water resistance and breathability if it is made of a hydrophobic polymer.
Protection Against Chemical Warfare Agents
Did you know that clothing with nanofibres is not only used by athletes, but also by elite soldiers? Scientists have recently discovered that nanofibre fabric can protect the body against warfare agents, such as chlorine, arsenic, or phosgene. This ability is crucial because it is chemicals like phosgene and arsenic that irreversibly damage skin and nerves.
Conventional protective clothing is based on the use of multi‑layered fabric with an extra protective layer. This usually consists of an inorganic material, such as activated carbon, which helps to trap dangerous chemicals and prevent them from penetrating the fabric. Although these conventional protective fabrics are still widely used, they have a high thermal load and are not air and water vapour permeable. The lack of breathability causes discomfort to the wearers and prevents them from actively performing their tasks.
Another disadvantage is the disposal of contaminated clothing. Conventional protective clothing is only able to physically adsorb the chemical, not detoxify it. This means that the clothing is heavily contaminated when it is removed and workers are exposed to hazardous chemicals when disposing of it.
Recent research has shown that metal oxides have excellent reactivity with chemical warfare agents and are also capable of detoxifying them.
Recently, the method of electrospinning of metal oxide nanofibres, which can then be incorporated into chemical protective clothing, has been increasingly used. Such clothing resists the penetration of organic molecules while being air and water vapour permeable. It will not make an elite soldier sweat or overheat, it will keep him perfectly warm and, at the same time, protect him from the penetration of life‑threatening chemicals.
Protection Against Microbes and Pathogens
Currently, antimicrobial garments are used in particular for healthcare workers, doctors, and other medical professions, and researchers are looking for the most effective way to make a lightweight, breathable, yet reliable fabric that will protect the wearer from invading bacteria and viruses.
Metal ions, usually silver, copper, and cadmium, are most commonly used to make antimicrobial fabrics because of their ability to deactivate bacteria. Silver is the most toxic to microorganisms and is, therefore, widely used in the manufacture of antimicrobial filters, dressings, air and water filters, and protective clothing. The cell‑ion of silver interaction causes structural changes in the cell that lead to the rupture of the cell wall and death of the bacterium.
Scientists developing nanofibre fabrics are also fascinated by silver. They either embed silver particles in the fibre matrix or coat the fibre surface with it. The small diameter of the fibres and the nanometre size of the silver particles provide an enormous surface area per unit volume of fibre. This helps to increase their antimicrobial effectiveness.
Currently, the effectiveness of silver‑coated nanofibres against Escherichia coli and Staphylococcus aureus is the most studied. Initial studies suggest that the fibres reduce metabolic activity and cell viability. It has also been shown that irradiation of the obtained fibres with UV light accelerates the formation of silver nanoparticles, and the nanofibres thus obtained have the greatest bactericidal effect.
Sources Used:
- https://www.ncbi.nlm.nih.gov/pmc/articles/PMC7077639/pdf/polymers‑12-00492.pdf,
- https://www.researchgate.net/publication/269356163_Protective_Clothing_Using_Nanofibers,
- https://pubs.rsc.org/en/content/articlehtml/2017/ra/c7ra04843b,
- https://www.cambridge.org/core/journals/journal‑of-materials‑research/article/abs/waterproof‑and-breathable‑polyacrylonitrilepolyurethanefluorinatedsilica-composite‑nanofiber-membrane‑via-sidebyside‑electrospinning/0CA307ADD9FEF5D72BA5051B36D2D4C6.